With the goal of reducing their temperature, an aftercooler for air compressor is employed to cool the air that has just left an air compressor. Through this action, the temperature can be decreased to a safe level for any accessories and steps that come afterwards. Here, this article will explain why using an aftercooler is advantageous for air compressors, its method of operation, and how it can be used.
Maximizing Efficiency of Air Compressors Through the Use of an Aftercooler
Atmospheric air is taken in by an air compressor with the aim of compressing it to a high pressure and transmitting the resultant compressed air for a myriad of applications. Nevertheless, during the pressurization process, the temperature is raised markedly which can disrupt the accuracy of downstream equipment operations as well as the stature of the pressurized air. Subsequently, using an aftercooler in conjunction with an air compressor makes available several enhancements; prominent among these are:
1. Shielding downstream paraphernalia: Compressed air with a high temperature can wreak havoc on downstream components such as air dryers, air filters, and pneumatic tools. Thankfully, an aftercooler can be used to reduce the temperature of compressed air and consequently shield these pieces of equipment from harm.
The use of an aftercooler for air compressors can boost the efficacy of a compressed air system by reduction of energy needed to store and transport the air that has gone through compression. This occurs due to the decrease in volume when compressed air is cooled.
Increasing the superiority of compressed air: Eliminating the moisture and unwanted pollutants through chilling the air before compressing it can drastically optimize the quality of the supplies and prevent any downstream processes from being detrimentally affected in a negative way.
What’s Inside an Aftercooler for Air Compressors?
A heat exchanger within an aftercooler for air compressors allows for the cooled, compressed air to escape downstream for various uses. Using a series of tubes, ambient air or even water is passed through, transporting heat away from the compressed air. The cooling medium does the heavy lifting by shifting the heat from the heat exchanger, resulting in the soothing cooling of the compressed air at last.
Cooling Down Air Compressors with the Application of Aftercoolers
Countless industrial operations rely onair compressors equipped with aftercoolers. These solutions are implemented for a wide array of tasks, from operation of air hammers to the creation of vacuums. Among the uses of aftercoolers is:
To safeguard pneumatic devices, for example, drills, sanders, and grinders, from extreme heat-related harm, aftercoolers are installed.
For efficient cooling, aftercoolers are incorporated into air conditioning and refrigeration systems to reduce the temperature of the compressed refrigerant prior to its usage in the chill cycle.
To ensure a glossy and polished finish for painting and coating projects, aftercoolers are a crucial tool to help filter out moisture and dangerous contaminants from the compressed air.
By employing an aftercooler for air compressors, users reap a myriad of advantages such as shielding downstream tools, augmenting efficiency and guaranteeing higher quality compressed air. The operation of an aftercooler is achieved by conveying compressed air through a heat exchanger where it is cooled down by water or ambient air. Aftercoolers are extensively employed over numerous industrial domains–from pneumatic tools and refrigeration and conditioning systems to coating and painting tasks. Using a suitable aftercooler for all air compressor operations, keeps the use of compressed air safe and economical.
Post time: 2023-06-10Related Product
Warning: Use of undefined constant rand - assumed 'rand' (this will throw an Error in a future version of PHP) in /www/wwwroot/www.sunritamachinery.com/wp-content/themes/msk5/single.php on line 69
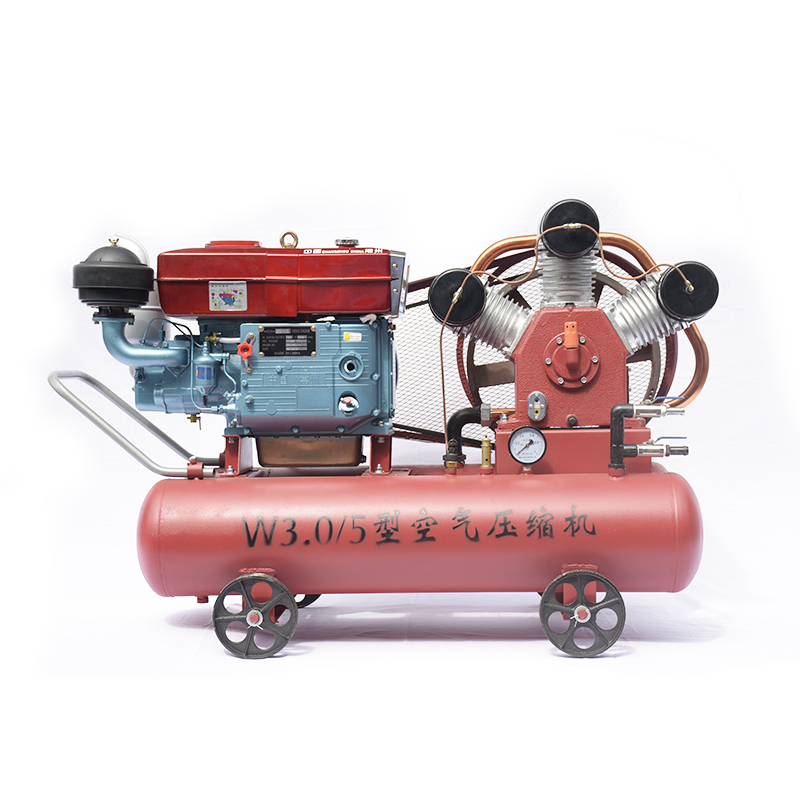
15kW Mining Diesel Piston Air Compressor W3.0-5
Diesel Portable Piston Air Compressor Mobile for Jack Hammer / Mining 1.Simple structure,light weight,easy to move . 2.Easy operating and maintenance. 3.High quality air delivery. […]
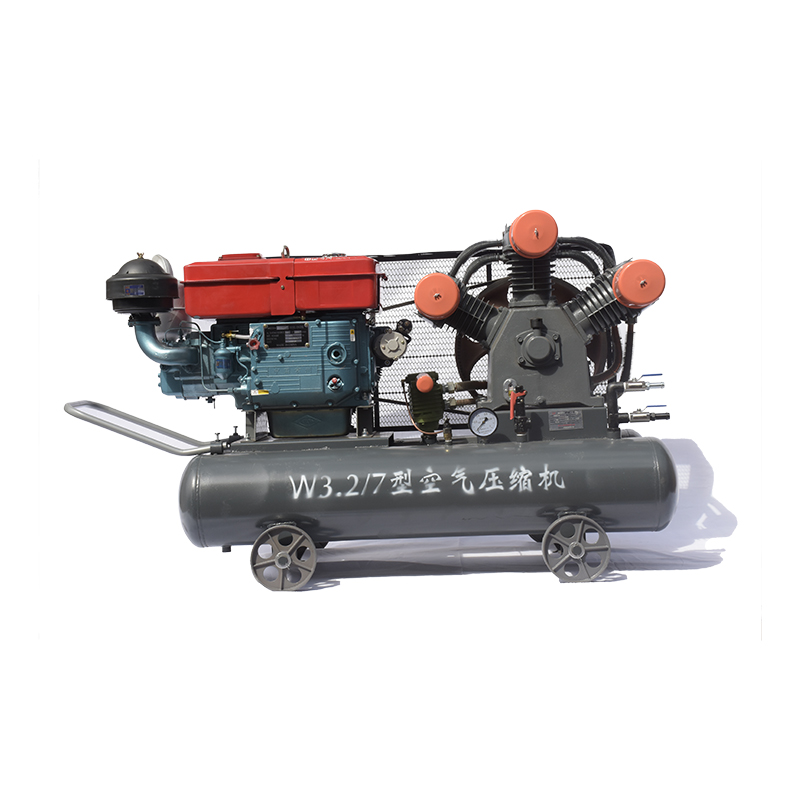
20KW Mining Diesel Piston Air Compressor W3.2-7
Advantages Small in size,light in weight, easy to move Top material and superior technology Simple structure, high efficiency, good performance, and low price Adopt the most popula […]
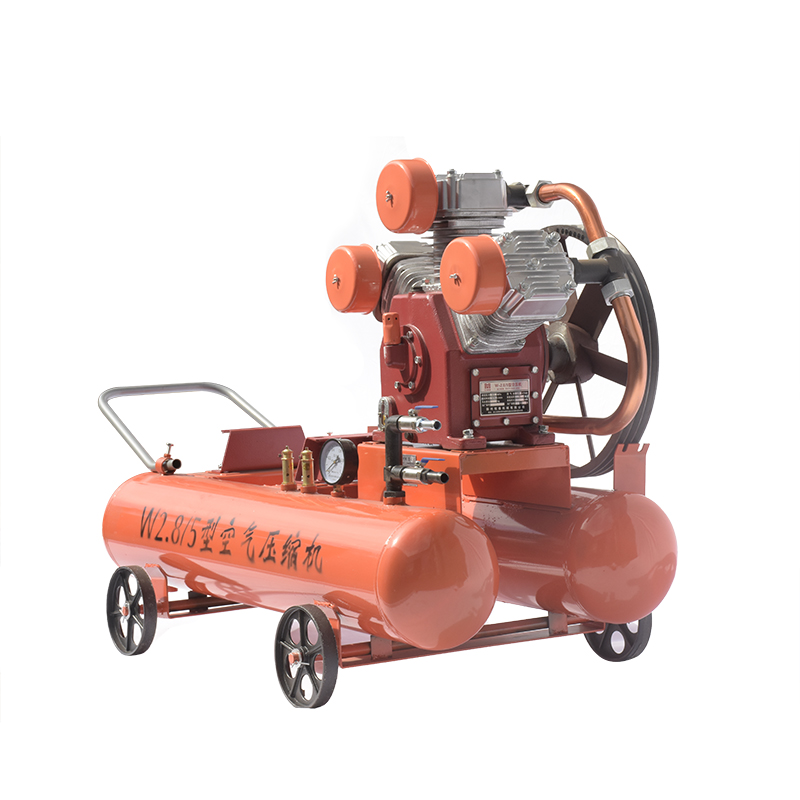
15KW Mining Diesel Piston Air Compressor W2.8-5
Diesel Portable Piston Air Compressor Mobile for Jack Hammer / Mining 1.Simple structure,light weight,easy to move . 2.Easy operating and maintenance. 3.High quality air delivery. […]
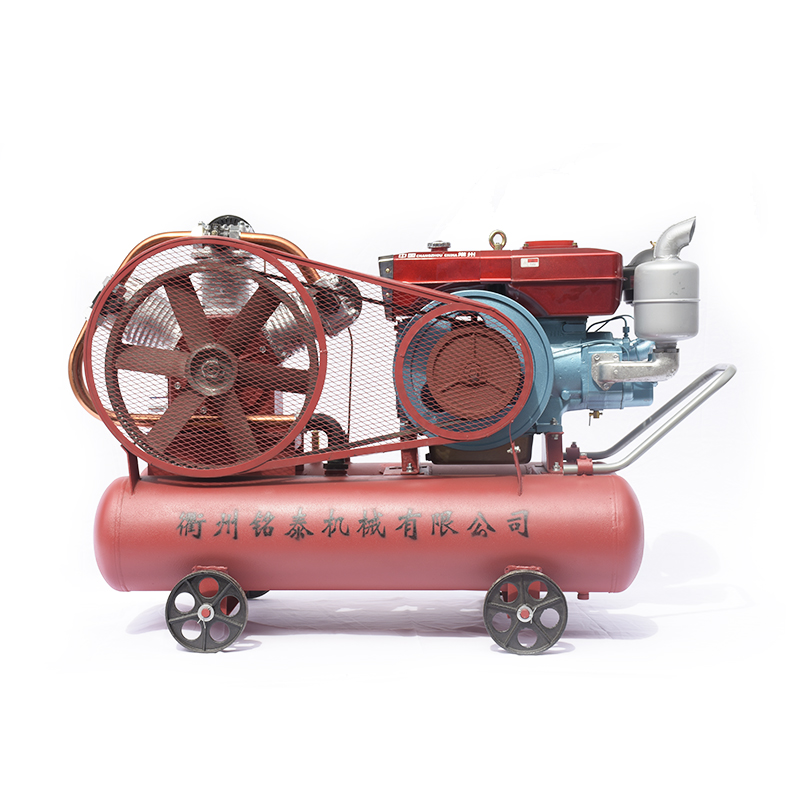
18.5KW Mining Diesel Piston Air Compressor W3.0-5
Advantages Small in size,light in weight, easy to move Top material and superior technology Simple structure, high efficiency, good performance, and low price Adopt the most popula […]
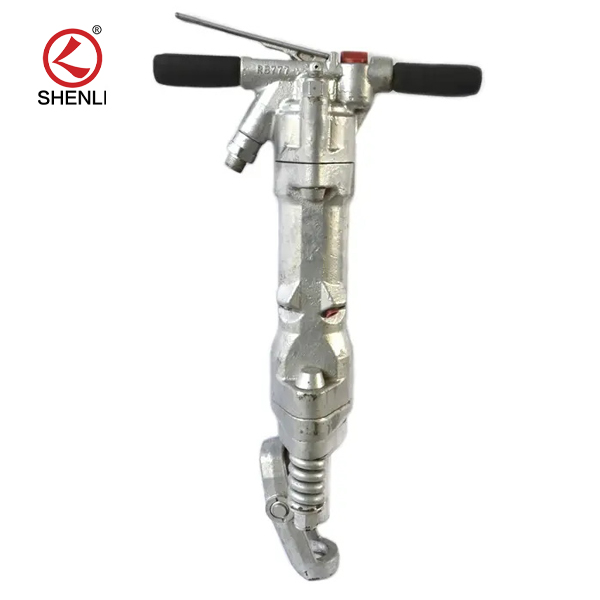
RB777 Pneumatic Pick Air Shovel Cement Crusher Pneumatic Chipping Hammer
Product description: RB777 pneumatic picks are used to build roads, install works of broken concrete and other hardens Hard object tools, the machine structure is simple, high effi […]
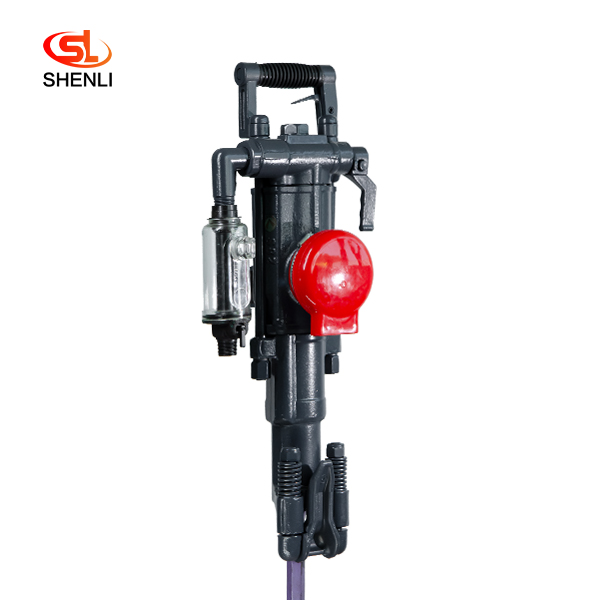
S82 Air Leg Pneumatic Rock Drill Pusher Leg Rock Drill
Scope of application: Model S82 air-legged rock drills are heavy-duty air-legged rock drills with high efficiency and low consumption, which are especially suitable for use in the […]
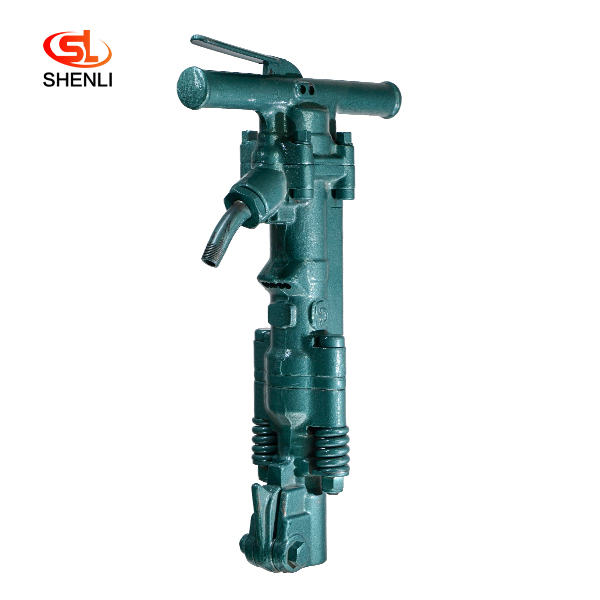
B47 Pneumatic Pick Air Shovel Cement Crusher Pneumatic Chipping Hammer
Product Description: B47 crusher adopts the mature technology of American Gardner Denver Pneumatic Group Company,It is a crushing tool powered by compressed air, which can finish r […]
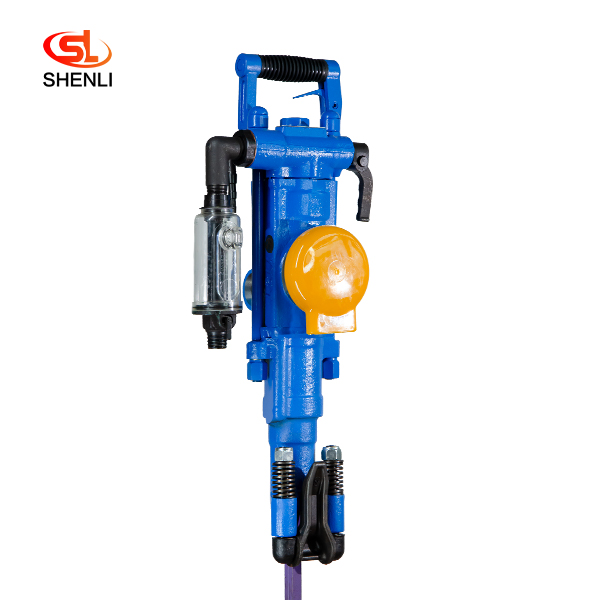
YT27 Air Leg Pneumatic Rock Drill
Short Description: The YT27 air-legged rock drill is a highly efficient lightweight rock drill suitable for downward or inclined drilling in medium-hard or hard (f=8 – 18) ro […]
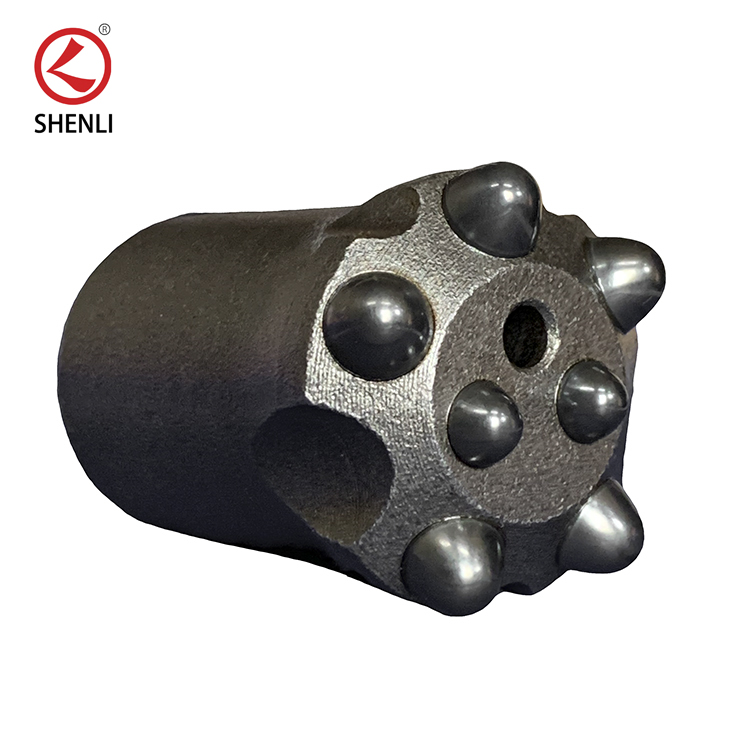
Rock Drill Button Bit
Product introduction: Taper bits, especially Tapered button bits are the most popular tapered drill bits with a wide selection of head diameters from 26mm to 48mm. With carbide but […]